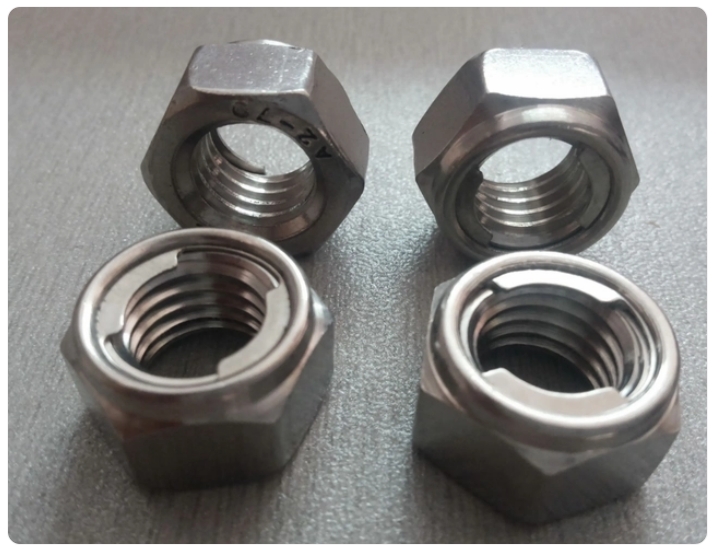
In mechanical equipment, fasteners are indispensable key components that securely connect various parts to ensure stable operation. Among these fasteners, flange nuts and locknuts play a vital role.
Firstly, let's discuss flange nuts. Flange nuts are special nuts with a flange disk, commonly used to connect pipes, valves, and other components. In mechanical equipment, the primary function of flange nuts is to provide powerful clamping force, ensuring tightness and stability between pipes, valves, and the equipment. Their unique flange design distributes the clamping force evenly, preventing damage to the equipment due to excessive local pressure. Additionally, flange nuts exhibit excellent corrosion resistance, adapting to various harsh working environments and ensuring long-term stable operation of mechanical equipment.
Next, we turn our attention to locknuts. Locknuts are fasteners with special locking mechanisms designed to prevent loosening due to vibration, impact, and other external forces. In mechanical equipment, locknuts are widely used in scenarios that require high vibration and impact resistance, such as engines and vibrating screens. Their locking mechanism maintains a secure clamping state, preventing equipment failures or accidents caused by loose nuts. Therefore, locknuts play a crucial role in enhancing the safety and reliability of mechanical equipment.
Beyond their basic functions, flange nuts and locknuts serve other vital roles in mechanical equipment. Firstly, they simplify the installation and disassembly process. Due to their excellent clamping and locking capabilities, they require minimal additional tools, improving work efficiency. Secondly, they reduce maintenance costs. Their long lifespan and stable performance minimize the need for frequent repairs and replacements, lowering overall maintenance expenses.
However, to fully leverage the crucial role of flange nuts and locknuts in mechanical equipment, several considerations are necessary. Firstly, selecting appropriate specifications and models is essential. Based on the equipment's specific requirements and operating environment, choosing suitable flange nuts and locknuts ensures their optimal performance. Secondly, proper installation and usage are crucial. Following product manuals and relevant regulations ensures correct installation and usage, preventing malfunctions or accidents due to improper handling. Finally, regular inspections and maintenance are vital. Regularly checking and maintaining flange nuts and locknuts in equipment ensures stable and reliable performance, extending the equipment's lifespan.
In conclusion, flange nuts and locknuts play a crucial role in mechanical equipment. They not only provide powerful clamping force and locking capabilities but also simplify installation and disassembly, reduce maintenance costs. Therefore, in the design and manufacturing of mechanical equipment, it is essential to fully consider the application needs and usage requirements of flange nuts and locknuts to ensure stable and safe performance of the equipment.