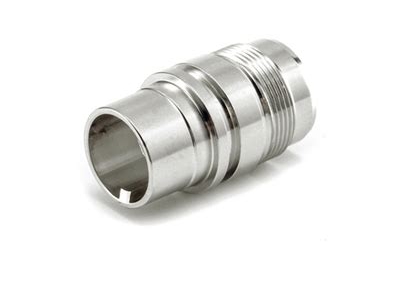
Introduction: Silver plating technology, known for its unique conductive and thermal properties, as well as excellent anti-corrosion and anti-oxidation characteristics, is widely used in various industries such as electronics, instruments, and lighting. This article will provide a detailed explanation of the optimal silver plating processes for different materials, helping you understand the advantages and applications of various plating methods, and offering support for your product selection and production.
1. Overview
Silver plating involves depositing a layer of silver metal onto the surface of other metals or non-metals to give the object specific properties. Depending on the substrate material, silver plating processes can be categorized into the following types:
1. Metal substrate silver plating
2. Plastic substrate silver plating
3. Ceramic substrate silver plating
4. Glass substrate silver plating
This article will compare the optimal silver plating processes for these four types of substrates, as well as their advantages and disadvantages.
2. Metal Substrate Silver Plating
Metal substrate silver plating refers to the silver plating process on metal substrates. Metal substrates have high conductive and thermal properties, and the plated silver layer offers good adhesion and anti-oxidation properties. Metal substrate silver plating is suitable for electronic products, sensors, connectors, and more.
The optimal process for metal substrate silver plating is chemical plating. Chemical plating has the following advantages:
1. The silver layer is uniform and dense with strong adhesion.
2. The process is simple and cost-effective.
3. Suitable for complex-shaped workpieces.
4. Environmentally friendly and pollution-free.
However, chemical plating has certain limitations, such as slower speed and higher water quality requirements.
3. Plastic Substrate Silver Plating
Plastic substrate silver plating refers to the silver plating process on plastic substrates. Plastic substrates are lightweight, abrasion-resistant, and corrosion-resistant, and the plated silver layer can improve the conductive and thermal properties of plastic products. Plastic substrate silver plating is suitable for various plastic products, such as plastic housings, plastic wires, and more.
The optimal process for plastic substrate silver plating is vacuum plating. Vacuum plating has the following advantages:
1. The silver layer is fine and smooth with strong adhesion.
2. The process is stable and repeatable.
3. Suitable for mass production.
4. Environmentally friendly and pollution-free.
However, vacuum plating equipment is expensive, and the surface treatment of the plastic substrate is required to be high-quality.
4. Ceramic Substrate Silver Plating
Ceramic substrate silver plating refers to the silver plating process on ceramic substrates. Ceramic substrates have high hardness, abrasion resistance, and corrosion resistance, and the plated silver layer can improve the conductive and thermal properties of ceramic products. Ceramic substrate silver plating is suitable for ceramic sockets, ceramic components, and more.
The optimal process for ceramic substrate silver plating is chemical vapor deposition (CVD) plating. CVD plating has the following advantages:
1. The silver layer is uniform and dense with strong adhesion.
2. The process is stable and repeatable.
3. Suitable for complex-shaped ceramic workpieces.
4. Environmentally friendly and pollution-free.
However, CVD plating equipment is expensive, and the surface treatment of the ceramic substrate is required to be high-quality.
5. Glass Substrate Silver Plating
Glass substrate silver plating refers to the silver plating process on glass substrates. Glass substrates have high transparency, hardness, and abrasion resistance, and the plated silver layer can be used to create high-end decorations and artistic glassware.
The optimal process for glass substrate silver plating is thermal diffusion plating. Thermal diffusion plating has the following advantages:
1. The silver layer is uniform and dense with strong adhesion.
2. The process is simple and cost-effective.
3. Suitable for mass production.
4. Environmentally friendly and pollution-free.
However, thermal diffusion plating requires high-quality surface treatment of the glass substrate, and the thickness of the silver layer is limited.
Conclusion
In summary, the optimal silver plating processes for different materials vary. When selecting a plating process, factors such as the application scenario, performance requirements, and cost budget of the product need to be comprehensively considered. At the same time, with the continuous development of technology, new silver plating processes are emerging, which can provide more options for product selection and production. It is recommended to consult with silver plating experts and manufacturers to determine the most suitable plating process for your specific needs.
By understanding the characteristics and advantages of various silver plating processes, you can make informed decisions to enhance the performance and functionality of your products. Whether you are in the electronics, instrument, or lighting industry, the right silver plating process can elevate your products to the next level.
Remember, the choice of silver plating process is crucial as it directly impacts the quality, cost, and market competitiveness of your products. With the right process in place, you can ensure that your products not only meet but exceed customer expectations.
End.