The Machining Process Schedule for Crank Arm Components
Time:2024-06-06 19:44:51 Source:未知 Click:次
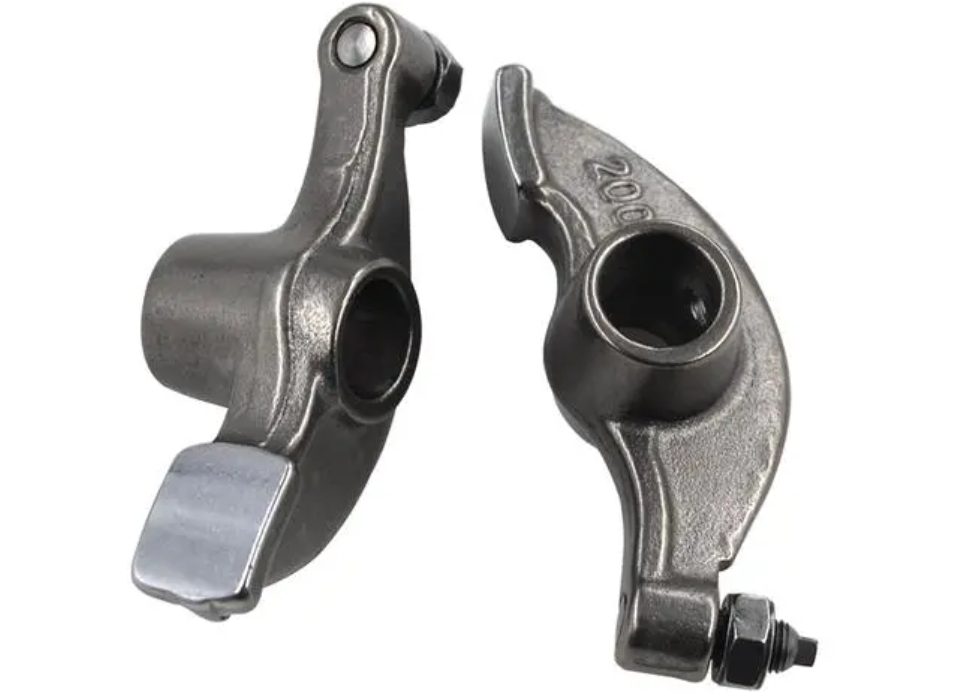
The crankshaft component is an essential part in mechanical equipment, primarily used for connecting the engine and transmission system, undertaking the critical tasks of engine vibration transmission and load bearing. Therefore, the quality of the crankshaft component directly affects the performance and service life of the entire mechanical equipment. This article will focus on the machining process specification for crankshaft components, introducing the manufacturing process, procedures, and important considerations for crankshaft components.
I. Machining Process of Crankshaft Components
1. Casting Process: Crankshaft components are typically made of cast iron or cast steel materials and are formed through the casting process. The casting process requires reasonable mold design, and control of temperature, time, and cooling rate during casting to ensure the dimensional accuracy, shape integrity, and uniform microstructure of the crankshaft components.
2. Machining Process: After casting, crankshaft components require mechanical processing to achieve the required dimensions, shapes, and surface quality as specified by the drawings. The machining process mainly includes the following aspects:
(1) Rough Machining: Rough machining is used to remove the excess material produced during the casting process, reducing the machining allowance in preparation for subsequent precision machining.
(2) Semi-Precision Machining: Through semi-precision machining, the dimensional, shape, and surface quality of the crankshaft components gradually approach the requirements of the drawings.
(3) Precision Machining: Precision machining processes, such as grinding, boring, and milling, are employed to finish the crankshaft components with high accuracy to meet the drawing requirements.
II. Machining Flow of Crankshaft Components
1. Inspection: Before machining, it is essential to inspect the cast crankshaft components for dimensional, shape, and microstructural conformity. If there are issues, adjustments should be made or the parts should be scrapped.
2. Rough Machining: Appropriate cutting parameters are used to remove excess material and reduce the machining allowance during rough machining. Attention should be paid to tool wear and dimensional changes in the workpiece.
3. Semi-Precision Machining: According to the drawing requirements, semi-precision machining is performed to gradually bring the dimensional, shape, and surface quality of the crankshaft components close to the specifications.
4. Precision Machining: High-precision processes such as grinding, boring, and milling are used for precision machining to meet the drawing requirements.
5. Heat Treatment: Based on the material and performance requirements, crankshaft components undergo heat treatment to improve hardness, strength, and wear resistance.
6. Surface Treatment: Surface treatments such as painting or plating are applied to crankshaft components to enhance corrosion resistance.
III. Considerations for Crankshaft Component Machining
1. Tool wear must be strictly controlled during the machining process, and tools should be replaced or sharpened in a timely manner to ensure quality.
2. Attention should be paid to the temperature changes of the workpiece to avoid dimensional errors caused by excessive or insufficient temperature.
3. In the precision machining stage, appropriate cutting parameters should be used to prevent cutting vibrations and surface scratches.
4. Strictly follow the process specification to ensure the stability of the machining process.
5. Inspect the machined crankshaft components to ensure that their dimensions, shapes, and surface quality meet the drawing requirements.
In conclusion, the machining process specification for crankshaft components is of great significance for ensuring their quality and the performance of the equipment. During the machining process, it is essential to adhere to the process specification, control each step meticulously, and improve the quality of crankshaft components and the service life of equipment. Additionally, continuously optimizing the machining process, improving production efficiency, and reducing costs contribute to the development of China's mechanical manufacturing industry.