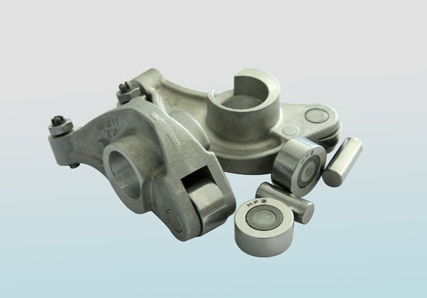
Introduction
Bearing rocker arms are crucial components in mechanical transmission systems, and their manufacturing process and quality control directly impact the performance and lifespan of the entire system. This article provides a detailed overview of the manufacturing process of bearing rocker arms and highlights key aspects of quality control to ensure products meet high-quality and high-performance standards.
I. Manufacturing Process of Bearing Rocker Arms
1. Material Selection
The manufacturing of bearing rocker arms typically uses high-strength alloy steel or premium carbon steel to ensure sufficient strength and wear resistance under high loads and complex stress conditions. Common materials include 40Cr and 45# steel.
2. Forging Process
2.1 Heating
The selected steel material first undergoes heating treatment to reach a suitable forging temperature range, usually around 1100°C. Uniform heating and precise temperature control are critical to ensuring the quality of the forged piece.
2.2 Forging
The heated steel is forged on a forging press, shaped through multiple hammerings and mold forming into the initial rocker arm blank. The rational design of the forging process and mold precision directly affect the quality of the blank.
3. Machining
3.1 Rough Machining
The forged blank undergoes rough machining, including removing surface oxidation, rough turning of the shape, and drilling holes. This stage lays the foundation for subsequent precision machining.
3.2 Precision Machining
Precision machining includes fine turning, milling, grinding, and drilling to ensure the dimensional accuracy and surface quality of various parts of the rocker arm. The surfaces in contact with the bearings particularly need to achieve high smoothness and precision.
4. Heat Treatment
Heat treatment is crucial for enhancing the performance of the rocker arm. Quenching and tempering are usually combined to achieve high hardness and good toughness. The hardened rocker arms undergo hardness testing to ensure they meet the expected performance requirements.
5. Surface Treatment
To enhance corrosion resistance and aesthetic quality, surface treatment is typically required. Common methods include galvanizing, spraying, and phosphating. Surface treatment not only improves the product's appearance but also effectively extends its service life.
II. Key Points of Quality Control
1. Material Inspection
Material selection is the first step in manufacturing bearing rocker arms, requiring strict inspection to ensure the composition and properties meet design requirements. Common inspection methods include spectrographic analysis, hardness testing, and ultrasonic flaw detection.
2. Forging Quality Control
Temperature control and mold precision during forging are key to ensuring the quality of the forged piece. It is essential to strictly control the heating temperature and forging parameters, regularly check mold wear, and ensure the dimensional accuracy and internal quality of the forged piece.
3. Machining Quality Control
During machining, critical dimensions must be strictly monitored using high-precision measuring tools to ensure dimensional accuracy and surface quality of all parts. Additionally, managing cutting fluids and tools during the machining process is crucial for maintaining process stability.
4. Heat Treatment Quality Control
Temperature and time control during heat treatment are vital. High-precision temperature control equipment should be used to monitor the quenching and tempering process in real-time, ensuring the rocker arm has uniform hardness and good toughness post-treatment.
5. Surface Treatment Quality Control
The cleaning, coating, and drying processes during surface treatment need strict control to ensure uniformity and adhesion of the surface treatment. Visual inspection and coating thickness testing are employed to check the quality of the surface treatment.
6. Final Product Inspection
A comprehensive quality inspection of the finished bearing rocker arms is performed, including dimensional measurement, hardness testing, and surface quality checks, to ensure the products meet design requirements and standards.
Conclusion
The manufacturing process of bearing rocker arms is complex, with numerous quality control points, and each process and step requires strict oversight. Through scientific process design and stringent quality control, high-quality bearing rocker arms can be produced, ensuring reliable operation in various mechanical transmission systems. It is hoped that the insights provided in this article can offer valuable reference for related professionals.