Concentricity: Key in Miniature Parts Machining
Time:2024-06-14 16:32:17 Source:未知 Click:次
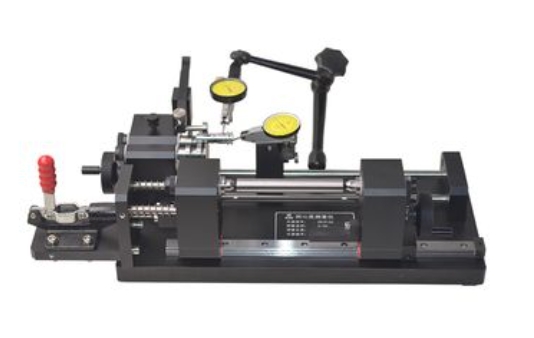
In the realm of miniature part machining, high precision concentricity is not only a guarantee of product quality but also the soul of precision manufacturing. The importance of this specification requirement is reflected in its significant impact on product performance, reliability, and ultimate user experience.
High precision concentricity refers to the degree to which the axis of a part matches its theoretical axis when rotating. For mechanical systems that require precise fit, such as gyroscopes, precision pumps, or high-end watches, the concentricity of components is directly related to the coordinated operation and lifespan of the entire system.
Achieving high concentricity during machining is extremely challenging. The condition of the machine tool, material stability, environmental control, and the technical level of operators all affect the final outcome. To this end, employing high-performance CNC machine tools and advanced detection equipment is a basic requirement. Optimizing machining processes, selecting the right cutting tools, and setting parameters are also crucial.
Maintaining high precision concentricity in the machining process of miniature parts can also reduce the need for post-correction and scrap rates, thereby saving costs and time. For instance, in the aerospace field, the stability of engine turbine blades at very high rotation speeds depends on the high concentricity of the parts. In the medical device field, the precise manufacturing of implantable devices such as heart pacemakers also requires strict control of concentricity.
As microminiaturization technology advances, the demands for concentricity are increasing. In the manufacture of micro-motors or miniature sensors, even deviations of a few micrometers can significantly compromise product performance. Therefore, fine machining technology continuously refreshes the control limits of concentricity, while also pushing up machining costs.
Maintaining high precision concentricity also involves the application of detection technology. Using precision instruments such as laser measurements and electronic callipers can monitor the concentricity of parts in real time, ensuring controllable machining processes. Additionally, quality management methods like Statistical Process Control can help manufacturers analyze data, optimize processes, and continuously improve the consistency of product concentricity.
The role of high precision concentricity in the machining of miniature parts cannot be overlooked. As industries demand greater precision, controlling concentricity will become even more critical. Manufacturers must continually invest in advanced technology and enhance process levels to ensure their products can stand firm in the fierce market competition.
In summary, high precision concentricity is one of the core elements in the machining of miniature parts, playing an irreplaceable role in ensuring product performance, reliability, and user satisfaction. With the advancement of technology and the increase in application requirements, the pursuit of concentricity control will continue to drive the manufacturing industry towards higher levels.