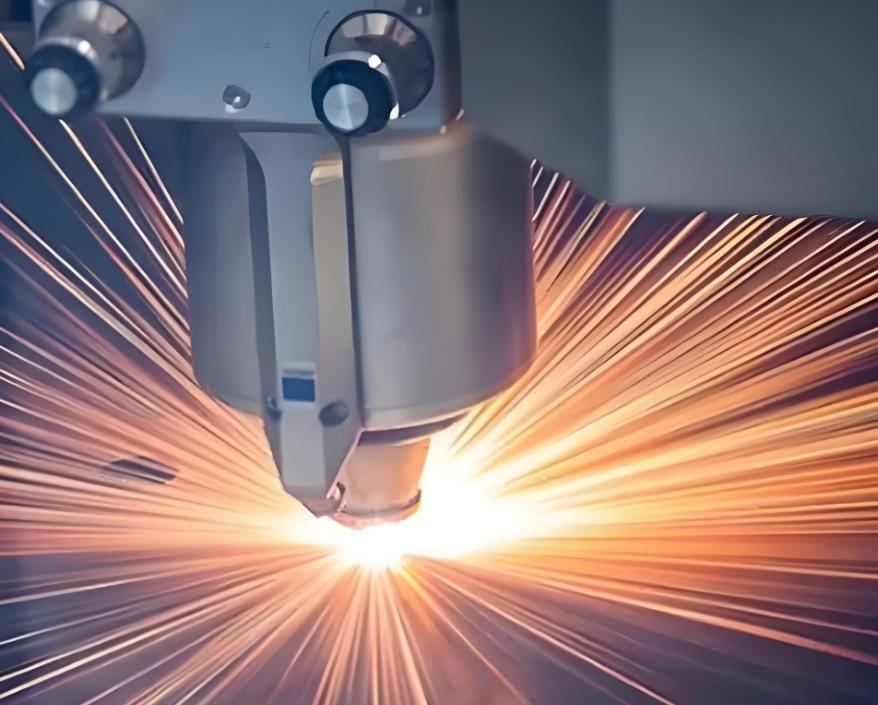
Introduction
Dissimilar metal welding technology plays a vital role in modern manufacturing. With the continuous advancement of technology and the increasing diversity of demand, dissimilar metal welding technology has become an indispensable processing method. This article will provide a detailed introduction to the basic principles, commonly used methods, and their applications in various industries.
Chapter One: Basic Principles of Dissimilar Metal Welding
Dissimilar metal welding refers to the process of joining different types of metal materials together through welding. The core of this technology lies in overcoming the differences in physical, chemical, and metallurgical properties between different metals to achieve stable and reliable connections.
1.1 Thermal Expansion Coefficient Difference
Different metals have different thermal expansion coefficients, which can lead to stress and deformation during welding. It is necessary to control welding parameters and processes properly to avoid crack formation and deformation in the weld joint.
1.2 Formation of Intermetallic Compounds
Certain metals are prone to form brittle intermetallic compounds at high temperatures, which can affect the mechanical properties of the weld joint. Suitable welding methods and fillers should be used to suppress or control the formation of these compounds.
1.3 Melting Point Difference
Different metals have significant differences in melting points, and proper control of heat input is required during welding to ensure the integrity and strength of the weld joint.
Chapter Two: Common Methods of Dissimilar Metal Welding
2.1 Melting Welding Method
2.1.1 Arc Welding
Arc welding is a common dissimilar metal welding method that connects metals by melting the welding rod and base material with an arc. To improve welding quality, special welding rods or wires are often used, and parameters such as current, voltage, and welding speed are adjusted.
2.1.2 Laser Welding
Laser welding is a technology that uses a high-energy laser beam as a heat source for welding, offering advantages such as high energy density, small heat-affected zone, and minimal distortion. It is suitable for high-precision and high-speed dissimilar metal welding.
2.2 Pressure Welding Method
2.2.1 Friction Welding
Friction welding joins metals by frictionally heating and plastically deforming the weld interface. This method is suitable for welding metals with a large melting point difference and has advantages such as high welding quality and speed.
2.2.2 Ultrasonic Welding
Ultrasonic welding uses high-frequency vibration energy to generate heat and plastic deformation at the contact interface, achieving the connection of dissimilar metals. This method is suitable for welding thin sheets and small components and has advantages such as fast welding speed and small heat-affected zone.
2.3 Brazing Method
Brazing connects dissimilar metals by using a filler material with a melting point lower than the base metals, which melts and fills the joint gap at high temperatures. Common brazing methods include soft brazing and hard brazing, suitable for different welding requirements.
Chapter Three: Applications of Dissimilar Metal Welding
3.1 Aerospace and Astronautics
Dissimilar metal welding is widely used in the aerospace and astronautics fields, manufacturing structural components and engine parts of aircraft and spacecraft. These parts require high strength, lightweight, and high-temperature resistance, which can effectively be met through dissimilar metal welding.
3.2 Automotive Manufacturing
In the automotive manufacturing industry, dissimilar metal welding technology is widely applied to the manufacturing of body structures, chassis systems, and engine components. By welding metals with different properties, the safety, fuel economy, and environmental protection performance of automobiles can be improved.
3.3 Electronics and Electricity
In the electronics and electricity industry, dissimilar metal welding technology is used in the manufacturing of circuit boards, connectors, sensors, and other devices. Due to the high requirements for welding quality and precision in electronic products, high-precision welding methods such as laser welding and ultrasonic welding are adopted to ensure product performance and reliability.
3.4 Petroleum and Chemical Industry
In petrochemical equipment, dissimilar metal welding technology is used to manufacture high-pressure vessels, heat exch