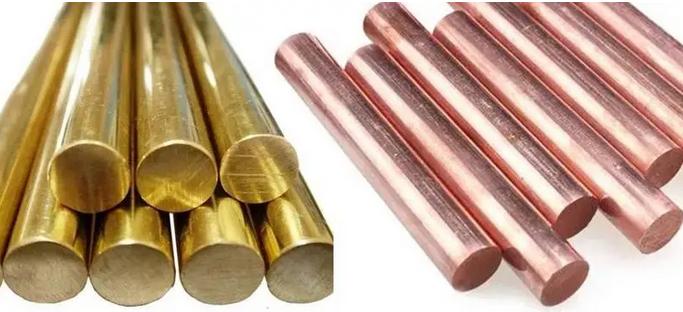
Copper and its alloys are widely used in industrial, construction, and electronic fields. Among them, brass and copper are two common copper alloy materials, each with unique physical and chemical properties. Oxidation resistance is an important performance indicator. This article delves into the oxidation resistance of brass and copper to provide a scientific basis for material selection.
I. Basic Characteristics of Brass and Copper
1.1 Brass
Brass is an alloy of copper and zinc. Based on zinc content, brass can be classified into common brass and special brass. Common brass usually contains 20% to 45% zinc, while special brass contains other alloying elements such as aluminum, tin, manganese, iron, and silicon.
- • Characteristics: Brass has excellent machinability, high strength, and good corrosion resistance, making it widely used in valves, water pipes, connectors, and decorative items.
- • Color: Due to the addition of zinc, brass appears yellow.
1.2 Copper
Copper, also known as red copper, primarily consists of copper, usually with a copper content of over 99.5% and minimal impurities. Based on the type and amount of impurities, copper can be further classified into oxygen-free copper, phosphorus-deoxidized copper, and common copper.
- • Characteristics: Copper has excellent electrical and thermal conductivity, good plasticity, and corrosion resistance, making it commonly used in electrical equipment, wires and cables, electronic components, and heat exchangers.
- • Color: Due to its high purity, copper appears reddish.
II. Comparison of Oxidation Resistance Between Brass and Copper
2.1 Oxidation Mechanism
When exposed to air, copper and its alloys react with oxygen to form oxides. Copper oxide (CuO) and cuprous oxide (Cu2O) are the main oxidation products. The oxidation resistance of copper depends on the stability and protective properties of these surface oxides.
2.2 Oxidation Resistance of Brass
The zinc in brass tends to oxidize easily in high temperature and humid environments, forming zinc oxide (ZnO). While zinc oxide provides some protection, high zinc content can reduce brass's overall oxidation resistance. Additionally, other alloying elements in brass can also affect its oxidation resistance. For example, aluminum-containing brass forms a stable aluminum oxide film at high temperatures, enhancing its oxidation resistance.
Examples:
- • Common Brass: High zinc content, relatively poor oxidation resistance.
- • Aluminum Brass: Special brass containing aluminum, with better oxidation resistance.
2.3 Oxidation Resistance of Copper
Due to its high purity, copper primarily forms Cu2O and CuO. These oxides form a dense oxide film on the copper surface, providing protection and preventing further oxidation. Particularly, oxygen-free copper, with minimal impurities, oxidizes more slowly and exhibits superior oxidation resistance.
Examples:
- • Oxygen-Free Copper: Nearly impurity-free, best oxidation resistance.
- • Common Copper: Though it contains some impurities, it still has better oxidation resistance compared to most brass types.
III. Practical Applications and Oxidation Treatments for Brass and Copper
3.1 Applications and Oxidation Treatments for Brass
Due to its high strength and wear resistance, brass is widely used in mechanical manufacturing, pipe fittings, and decorative materials. For applications requiring higher oxidation resistance, brass surfaces often undergo treatments such as electroplating, spraying, and chemical coating.
Treatment Methods:
- • Nickel/Chrome Plating: Electroplating a layer of nickel or chrome on brass surfaces significantly improves oxidation resistance.
- • Protective Coating: Spraying a transparent coating to isolate air and prevent oxidation.
3.2 Applications and Oxidation Treatments for Copper
With its excellent electrical conductivity and oxidation resistance, copper is widely used in electrical and electronic fields. To further enhance its oxidation resistance, copper surfaces can also undergo treatments like coating protection and vapor deposition.
Treatment Methods:
- • Chemical Passivation: Forming a stable passivation film on the copper surface to enhance oxidation resistance.
- • Coating Protection: Spraying a transparent protective film to further prevent oxidation.
IV. Conclusion
In terms of oxidation resistance, copper generally outperforms brass. This is mainly due to copper's high purity, forming a more stable oxide film that effectively prevents further oxidation. However, through alloying and surface treatment techniques, the oxidation resistance of brass can also be significantly improved.
In practical applications, material selection should be based on specific usage environments and performance requirements. For high oxidation resistance and stringent electrical conductivity needs, copper is preferable. For applications requiring high mechanical strength and wear resistance, appropriately treated brass is also a good choice. It is hoped that this article provides valuable reference for selecting copper alloy materials.