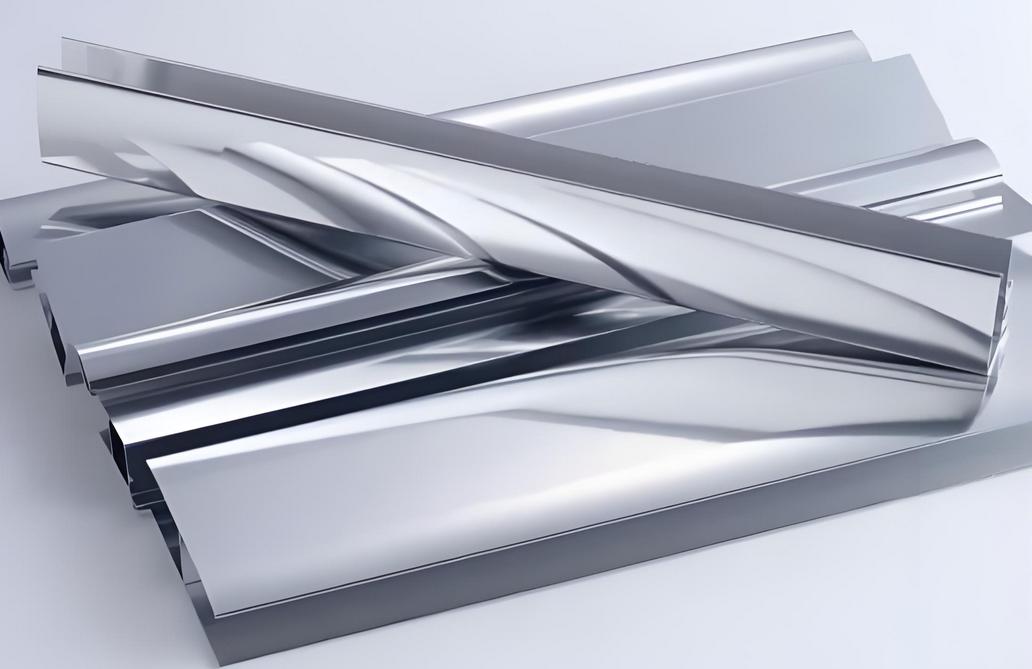
I. Characteristics and Applications of Conductive Oxidation Process
1. The conductive oxidation film has good electrical conductivity, meeting the requirements of electronic products for electrical conductivity.
2. The conductive oxidation film has good corrosion resistance, which can extend the service life of aluminum alloys in harsh environments.
3. The surface of the conductive oxidation film is smooth, and the color is uniform, offering a good aesthetic effect.
4. The electrolyte solution used in the conductive oxidation process can be recycled, causing less environmental pollution.
The conductive oxidation process is mainly used in the following aspects:
1. Electronic products: such as internal aluminum alloy components in mobile phones, computers, and televisions.
2. Power equipment: such as transformers.
3. Automotive parts: such as battery shells and motor shells of new energy vehicles.
II. Characteristics and Applications of Anodic Oxidation Process
1. The anodic oxidation film has good corrosion resistance, which can extend the service life of aluminum alloys in harsh environments.
2. The anodic oxidation film has good wear resistance, which can improve the wear resistance of the aluminum alloy surface.
3. The surface of the anodic oxidation film is smooth, and the color is uniform, offering a good aesthetic effect.
4. The electrolyte solution used in the anodic oxidation process can be recycled, causing less environmental pollution.
The anodic oxidation process is mainly used in the following aspects:
1. Building materials: such as aluminum alloy doors and windows, curtain walls, etc.
2. Decorative items: such as aluminum alloy furniture, lighting fixtures, etc.
3. Medical devices: such as surgical instruments, rehabilitation equipment, etc.
III. Guidelines for Choosing Conductive Oxidation and Anodic Oxidation
When choosing between conductive oxidation and anodic oxidation processes, it is necessary to judge based on the actual application scenarios and performance requirements. Here are some guidelines for selection:
1. If your product requires good electrical conductivity, such as internal components of electronic products, conductive oxidation is a better choice.
2. If your product needs good corrosion resistance and wear resistance, such as building materials or medical devices, anodic oxidation is a better choice.
3. If your product needs good aesthetic effects, both processes can meet the requirements. However, the film layer produced by conductive oxidation is thinner, with relatively fewer color options; the film layer produced by anodic oxidation is thicker, with more color options.
4. In terms of environmental protection, both processes can recycle the electrolyte solution, causing less environmental pollution.
In summary, both conductive oxidation and anodic oxidation processes are excellent surface treatment technologies for aluminum alloys. In practical applications, the appropriate process should be selected based on the performance requirements and application scenarios of the product.