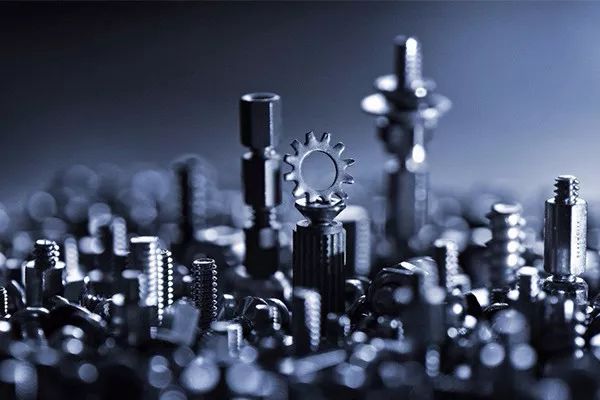
1. Common Materials for Bolt Processing
Material selection for bolts is based on their strength classes: the most common materials for standard fasteners in the market are carbon steel, stainless steel, and copper.
▌Carbon Steel
Carbon steel is categorized based on the carbon content in the material, which includes low-carbon steel, medium-carbon steel, high-carbon steel, and alloy steel.
A. Low-carbon steel: C% ≤ 0.25%, commonly referred to as A3 steel in China. In foreign markets, it is generally known as 1008, 1015, 1018, 1022, etc. It is primarily used for products without hardness requirements, such as 4.8-grade bolts, 4-grade nuts, and small screws. (Note: Self-drilling screws typically use 1022 material.)
B. Medium-carbon steel: 0.25% < C% ≤ 0.45%. Domestically known as 35 and 45 steel, and abroad as 1035, CH38F, 1039, 40ACR, etc. It is mainly used for 8-grade nuts, 8.8-grade bolts, and 8.8-grade hexagonal internal products.
C. High-carbon steel: C% > 0.45%. Currently, it is scarcely used in the market.
D. Alloy steel: Alloy elements are added to plain carbon steel to enhance certain special properties, such as 35, 40 chrome molybdenum, SCM435, 10B38. Fang Sheng screws primarily use SCM435 chrome molybdenum alloy steel, with main components including C, Si, Mn, P, S, Cr, and Mo.
▌Stainless Steel
Stainless steel is categorized by its performance grades.
A. Grades 45, 50, 60, 70, 80 mainly include austenite (18% Cr, 8% Ni) with good heat resistance, corrosion resistance, and weldability.
B. Grades A1, A2, A4 mainly include martensite with 13% Cr, which has poor corrosion resistance, high strength, and good wear resistance.
C. Grades C1, C2, C4 are ferritic stainless steels with 18% Cr. They have better forging properties and a higher corrosion resistance than martensite.
D. Imported materials in the market are primarily Japanese products, mainly categorized as SUS302, SUS304, SUS316 based on their grades.
▌Copper
The commonly used materials for copper fasteners are brass and zinc-copper alloys. The market mainly uses H62, H65, H68 copper for standard parts.
2. Spheroidizing (Softening), Annealing
1) Spheroidizing (softening) annealing is applied to countersunk bolts and hexagonal head bolts produced by cold upsetting. The original microstructure of the steel directly affects the forming capability during cold upsetting.
2) During the cold upsetting process, the plastic deformation in local areas can reach up to 60%-80%. Therefore, the steel must have good plasticity. When the chemical composition of the steel is constant, the microstructure is the critical factor determining the plasticity, with coarse and large flake pearlite being disadvantageous for cold upsetting, while fine spherical pearlite can significantly improve the steel's plastic deformation capacity.
3) For medium carbon steels and medium carbon alloy steels commonly used in high-strength fasteners, spheroidizing (softening) annealing is performed before cold upsetting to obtain a uniform and fine spheroidite pearlite, better meeting the actual production needs.
4) For medium carbon steel wire rod softening annealing, the heating temperature is often chosen around the critical point of the steel, and the temperature should not be too high, otherwise, carbides will precipitate along the grain boundaries during cooling, leading to cold upsetting cracking.
5) Medium carbon alloy steel wire rods are annealed using the isothermal spheroidizing process, heated to AC1+(20-30%) and then cooled to slightly below Ar1, around 700°C isothermal for