Spanning our country's vast expanse of 9.6 million square kilometers, China's railway mileage has reached 159,000 kilometers. This extensive railway network is connected by countless steel rails of different lengths.
Once limited by technological conditions, each steel rail was only 25 meters long, with about an 8mm gap left at each joint to accommodate the expansion and contraction of the rails due to heat and cold. Since each rail was of equal length, the wheels would produce a rhythmic clanging sound when they reached the gap. Over time, this sound gradually became the iconic sound of trains in people's memories.
The "Evolution" of Rails Makes the Train's "Clanging" Sound Disappear
Is it possible to make the rails seamlessly join? In 1958, the main railway line from Beijing to Tianjin used air pressure welding to lay 200 meters of seamless track, marking the first time that long welded rails were used on a main line railway.
Over the past 60-plus years, China has successively developed technologies such as rail aluminum thermite welding, air pressure welding, and flash welding. Simply put, these technologies are mainly aimed at solving one problem: making the rail joints increasingly tight. What does this mean? It's like after the rails are welded, they form a seamless whole, and the clanging sound of the wheels passing over the welded parts is basically eliminated.
Are there other methods to reduce noise and increase speed besides seamless joints? The most fundamental method is to extend the length of a single rail. In the China Railway Museum, there is a preserved "century-old rail" from 1901, which is only 675 mm long. In old China, with backward industry, such was the length of the rails that could be produced.
Nowadays, in the production workshop of Angang Steel, the heavy rail production line is continuously pushing the limits of industry, with the standard length of rails increasing from 25 meters to 50 meters, and then to 100 meters! Taking the 100-meter long standard rail as an example, the flatness deviation does not exceed 0.5 mm, representing the highest international level. Through seamless welding, the rails are connected into a single entity. Thus, the "clang, clang" sound has become a historical echo.
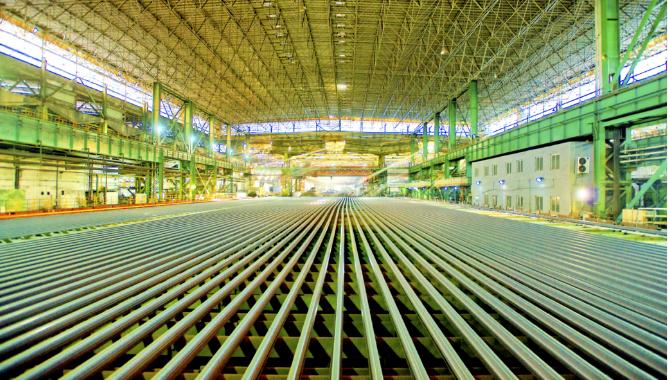
▲ Angang's 100-meter long standard rail, with world-class level
Especially for high-speed railways, seamless tracks were adopted from the initial design stage. The factory length of the rails is 100 meters, which, after being transported to the welding plant, are processed and welded into 500 meters. Subsequently, the rails are transported to the laying site by rail transport vehicles, where railway workers lay them on the track and perform secondary welding, ultimately forming a seamless railway.
PART 3 How to Solve the Issue of Expansion and Contraction? Facing the challenge of changing from jointed to seamless rails, the railway department determines the minimum and maximum rail temperatures based on the historical temperatures of the area where the line is located, calculating the locked rail temperature. The locked rail temperature is the temperature at which workers use bolts (screws) bent into fasteners to fix the rails.
When laying and welding rails, efforts are made to choose the moderate temperatures of spring and autumn, and the actual rail temperature is measured before laying to confirm whether it meets the locked rail temperature range requirements. If the requirements are not met, the rails undergo a release treatment to evenly release the internal physical forces. Then, the rails are fastened with fasteners to ensure that they will not produce expansion or contraction displacement under the influence of temperature changes.
In some special sections, such as high-cold areas with large temperature differences, expansion joints are also installed on the rails to ensure that the line remains smooth and stable.