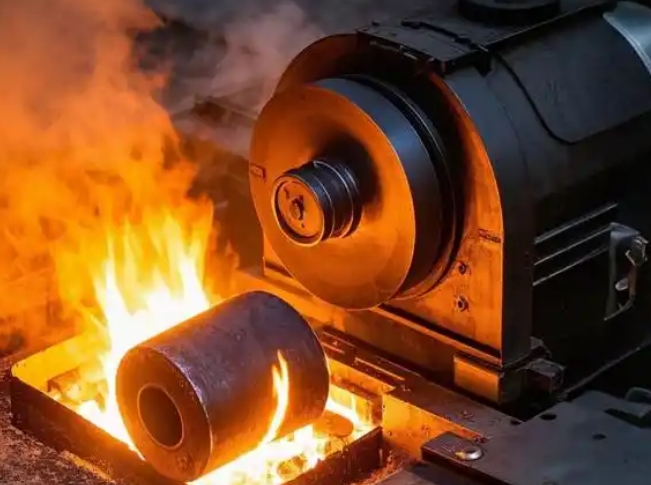
In modern industrial production, the application of high-strength fasteners is increasingly widespread, and the quality of these fasteners directly affects the safety and performance of mechanical equipment. This article will delve into the heat treatment process of high-strength fasteners and reveal the important role of quenching and tempering in enhancing the comprehensive mechanical properties of these fasteners.
Quenching and Tempering: An Essential Process for High-Strength Fasteners
High-strength fasteners must undergo quenching and tempering during production according to technical requirements. Quenching and tempering is a type of heat treatment process aimed at improving the comprehensive mechanical properties of fasteners to ensure that the products meet the specified tensile strength values and yield ratios. This process is significant for enhancing the durability and reliability of fasteners.
The Impact of Heat Treatment on the Intrinsic Quality of Fasteners
The heat treatment process has a crucial impact on the intrinsic quality of high-strength fasteners. To produce high-quality high-strength fasteners, a company must be equipped with advanced heat treatment technology and equipment. This is because the heat treatment process can alter the internal structure of metal materials, thereby affecting their properties.
Requirements for Heat Treatment Equipment
Due to the large production volume and low cost of high-strength bolts, as well as the intricate and precise structure of the thread section, heat treatment equipment must possess the following characteristics: large production capacity, high degree of automation, and good heat treatment quality. This ensures that the produced fasteners meet market demands.
The Issue of Thread Decarburization and Its Impact
Thread decarburization is a major challenge in the production of high-strength fasteners. Decarburization can cause the fastener to strip before reaching the required mechanical strength, leading to failure and shortened service life. Improper decarburization of raw materials and improper annealing can exacerbate this issue. The introduction of oxidizing gases during the quenching and tempering process can also intensify decarburization.
Discussion on the Degree of Decarburization
Studies have shown that the degree of decarburization in medium-carbon alloy steel is more severe than in carbon steel, with the fastest decarburization occurring at temperatures between 700-800 degrees Celsius. The decomposition of surface contaminants on steel wire into CO2 and H2O can be rapid under certain conditions, and improper control of the furnace atmosphere can also lead to excessive decarburization of screws.
Cold Heading and Quenching Issues
When high-strength fasteners are formed using cold heading, the decarburization layer of the raw material and annealing is compressed to the top of the thread, resulting in insufficient surface hardness after quenching and reduced mechanical properties. Additionally, surface decarburization of the steel wire can lead to surface cracks during quenching.
Quality Issues During Quenching and Tempering
Quality issues that may arise during the quenching and tempering process of fasteners include insufficient hardness in the quenched state, uneven hardness in the quenched state, excessive quenching deformation, and quenching cracks. These issues are often related to the raw materials, quenching heating, and quenching cooling.
How to Avoid Quality Accidents
To avoid the aforementioned quality accidents, companies should correctly formulate heat treatment processes and standardize production operation procedures. By strictly controlling heat treatment parameters, the quality of fasteners can be ensured to meet expected targets.
In conclusion, the heat treatment process of high-strength fasteners plays a decisive role in their performance. Only by mastering advanced heat treatment technology can high-quality fasteners be produced, providing a strong guarantee for the development of our country's industry.