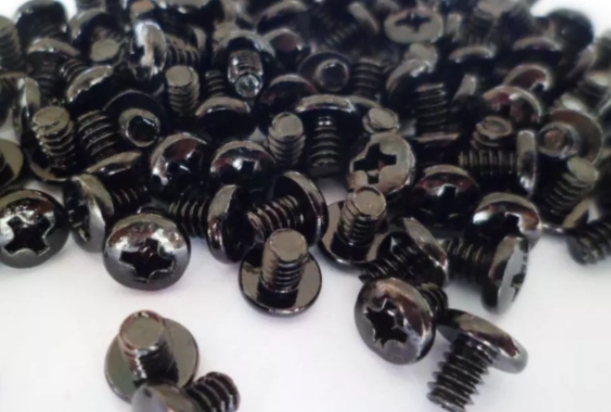
In the world of fasteners, the surface treatment of screws is a critical aspect that not only affects their appearance but also their functionality and durability. Among the various surface treatment processes, oxidation, electrophoresis, electroplating, and dacromet are the most commonly used. In this article, we will categorize these processes based on the color of the screw surface, with a focus on black screws.
Black screws are predominantly used to secure the bottom or back shells of black or other dark-colored electrical appliances. They are also commonly used inside machines to minimize the complexity of parts management. The main surface treatment processes for black screws include oxidation black, black nickel, black zinc, and electrophoretic black.
Oxidation Black:
Oxidation, also known as anodizing, is a process that creates a layer of oxide on the surface of the screw. For black screws, this process results in a deep, matte black finish that is both aesthetically pleasing and corrosion-resistant. Oxidation black screws are ideal for applications where a sleek, non-reflective surface is desired, and they are often used in high-end electronic devices.
Black Nickel:
Black nickel plating is a process that involves coating the screw with a layer of nickel alloy that has a black appearance. This finish provides a smooth, lustrous black surface that is more resistant to wear and corrosion than standard nickel plating. Black nickel screws are commonly used in automotive and aerospace industries where both durability and a specific aesthetic are important.
Black Zinc:
Black zinc plating, also known as black passivation, is a process that involves applying a layer of zinc followed by a black chromate conversion coating. This results in a durable, black finish that offers excellent corrosion resistance. Black zinc screws are widely used in outdoor applications and in environments where exposure to moisture is a concern.
Electrophoretic Black:
Electrophoretic painting, or e-coating, is a process where electrically charged particles are deposited onto the screw's surface. The result is a uniform, black coating that is highly resistant to corrosion and offers a smooth finish. Electrophoretic black screws are commonly used in the automotive industry due to their ability to cover complex shapes and provide a consistent color.
Each of these black surface treatments has its own advantages and is chosen based on the specific requirements of the application. For instance, oxidation black might be preferred for its matte finish, while black nickel could be chosen for its luster and wear resistance.
In conclusion, the choice of surface treatment for black screws is not merely aesthetic; it is a careful consideration of the environment in which the screw will operate, the level of corrosion resistance required, and the overall durability needed. By understanding the different processes and their outcomes, manufacturers and consumers can make informed decisions that ensure the screws meet the demands of their intended use. Whether it's for the sleek look of a high-tech gadget or the rugged performance of outdoor equipment, the right surface treatment can make all the difference.