Eastec build e-cigarette heater and battery chamber from 2017, easy to find the IQOS high quality cosmetic appearance and smooth touch feeling parts in speciality stores. For all manufactures, appearance standard components are challenges from defect identify-define-control-inspection,
every step means cost, from uniformity feature, color,roughness and gloss shining, all including one key feature-Aesthetic standard. From Eastec experience, we list some cosmetic defect phenomena below and try to give some root causes sharing.
1) Aluminum Alloy material problem including 3 typical indexes,Alloy uniformity difference,Silicon precipitation and material batch difference. High quality cosmetic parts comes from high quality material. Defect parts show out ugly lines in outer surface often comes from raw material failing.
2) Aluminum Alloy extrusion defect, welding-line and extrusion-process parameters cause potential cosmetic failure such as visible lines defect and orange-skin defect. Even worse, the defect issues can’t remove although after further polish process. The defect cause material waste in reality.
3) Physical scratch in machining, Aluminum Alloy material is soft and easy destroy in tiny touch, in all manufacturing loop, keep clean and protect the surface is vital for higher rate of quality.
4) Polish solution, some parts request polish to get higher cosmetic standard. Neglect micro hole defect may turn to honeycomb defect after anodizing process.
5) Sand blasting process,sand quality, sand mesh,basting pressure, flow solution etc determine the final surface-finish-quality, Sand blasting may solve some of former phase failures.
6) Anodizing quality,the most important step to show out final part cosmetic quality. Including oil clean-deep clean-surface active-coloring-drying, in the full flow, every step is vital to final quality standard. Operators involves a lot in the real laboring, every plants own self secret on parameters.
7) Inspection cycle,sorting out defect parts is the last step for OQC control. First-Pass-Yield rate is the benchmark of the project win-lost.
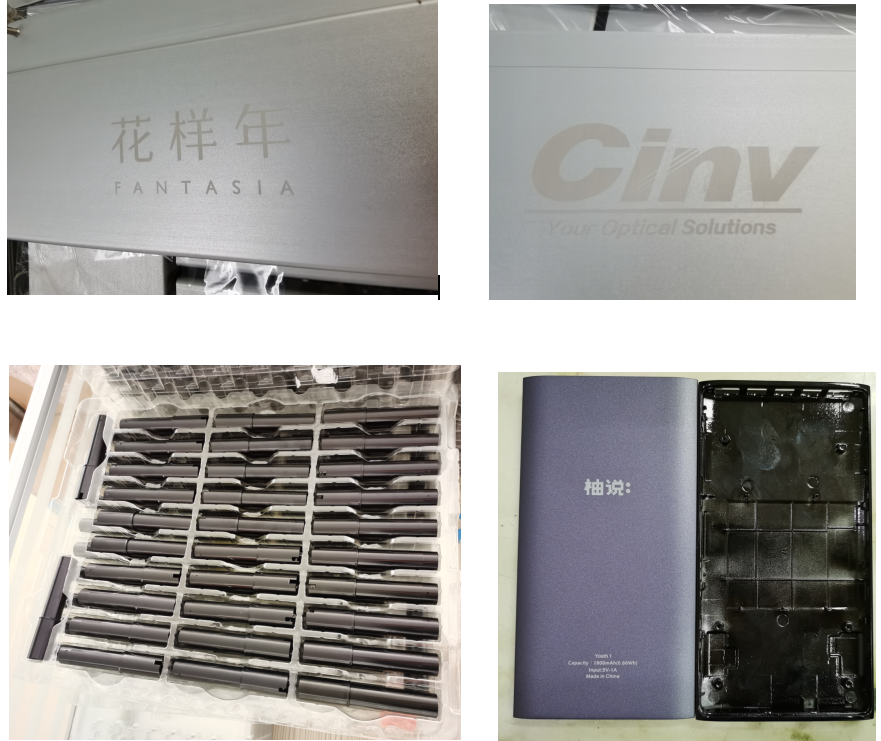