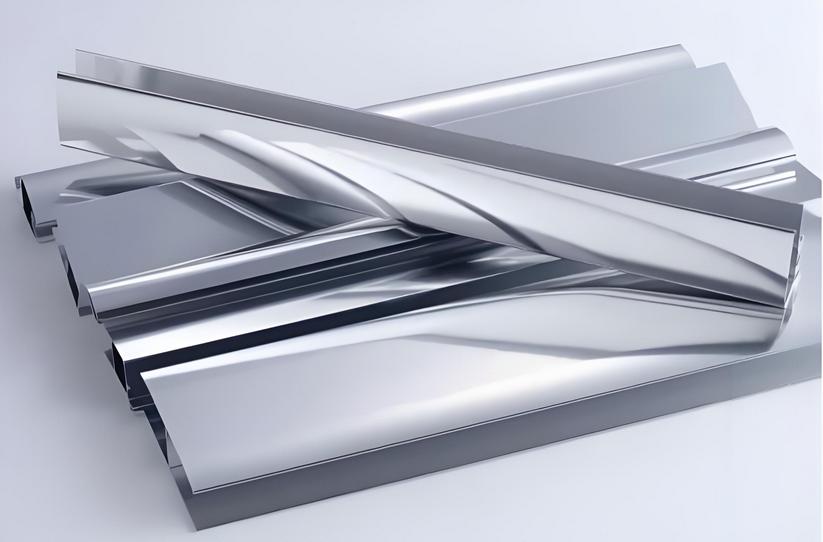
1. Conductive Oxidation
Conductive oxidation is a technique that forms a conductive oxide film on the surface of aluminum alloys. This oxide film has good conductivity, corrosion resistance, and adhesion. The process of conductive oxidation is relatively simple, mainly involving a chemical reaction at room temperature to produce an oxide film on the surface of the aluminum alloy. This method requires less equipment and is relatively low cost.
The advantages of conductive oxidation include:
1. Good conductivity: The conductive oxide film has good conductivity, suitable for applications requiring electrical conductivity.
2. Corrosion resistance: The conductive oxide film has good corrosion resistance, which can extend the service life of aluminum alloys.
3. Adhesion: The conductive oxide film has good adhesion, which can improve the bonding strength between aluminum alloys and other materials.
2. Anodizing
Anodizing is a technique that forms a dense oxide film on the surface of aluminum alloys. This oxide film has high hardness, corrosion resistance, and wear resistance. The process of anodizing is more complex, requiring the surface of the aluminum alloy to be oxidized into an oxide film under a certain voltage. This method requires higher equipment standards and is relatively more expensive.
The advantages of anodizing include:
1. High hardness: The anodized film has high hardness, which can improve the wear resistance of aluminum alloys.
2. Corrosion resistance: The anodized film has excellent corrosion resistance, effectively preventing corrosion on the surface of aluminum alloys.
3. Aesthetics: The anodized film has a rich color and gloss, enhancing the appearance quality of aluminum alloys.
3. Differences and Advantages Analysis
1. Process: Conductive oxidation forms an oxide film through a chemical reaction at room temperature, while anodizing requires a certain voltage.
2. Effects: The conductive oxide film has better conductivity, corrosion resistance, and adhesion, while the anodized film has better hardness, corrosion resistance, and aesthetics.
3. Application areas: Conductive oxidation is suitable for applications requiring electrical conductivity, such as electronic components and electrical equipment; anodizing is suitable for applications requiring high hardness, corrosion resistance, and aesthetics, such as decorative materials and building supplies.
4. Cost: Conductive oxidation requires lower equipment standards and is relatively low cost; anodizing requires higher equipment standards and is relatively more expensive.
In summary, conductive oxidation and anodizing differ in the process, effects, and application areas. The choice of technique should be based on actual needs and cost considerations. For applications requiring good electrical conductivity, corrosion resistance, and adhesion, conductive oxidation is a good choice; for applications requiring high hardness, corrosion resistance, and aesthetics, anodizing is more suitable.