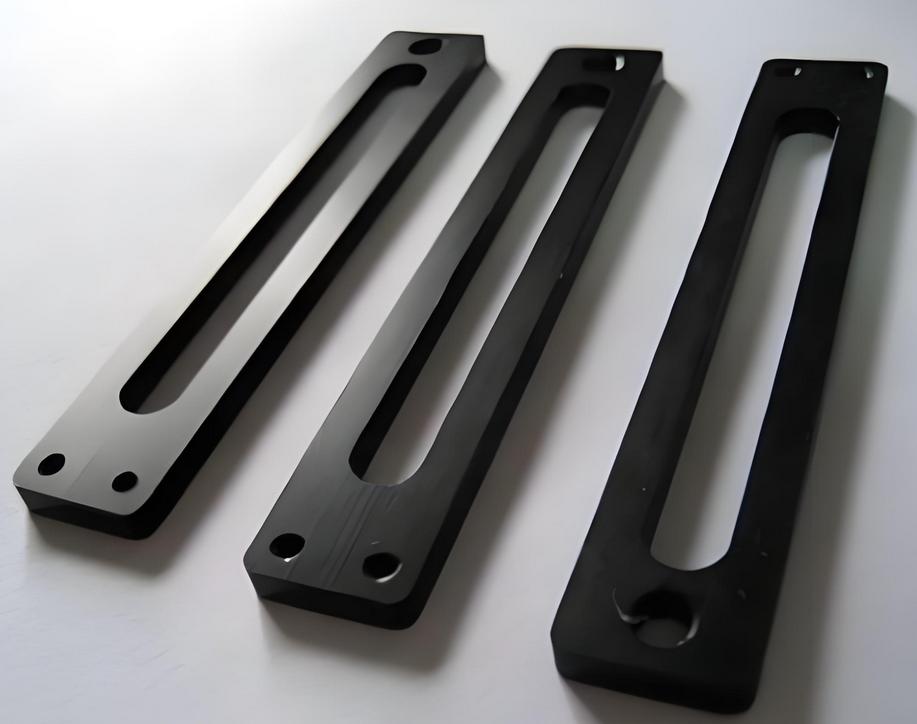
I. Conductive Oxidation Process
Conductive oxidation, also known as anodic oxidation, is a process that forms a conductive oxide film on the surface of aluminum alloys. This process occurs in a specific electrolyte solution, where, through the action of an electric current, an oxidation reaction takes place on the surface of the aluminum alloy, forming a dense oxide film. The conductive oxide film possesses excellent conductivity and corrosion resistance, improving the electrical conductivity and corrosion resistance of aluminum alloys.
The principle of the conductive oxidation process involves the use of an electrolyte solution, where the aluminum alloy acts as the anode, undergoing oxidation due to the electric current. Anions in the electrolyte solution accumulate near the anode and combine with metal ions on the surface of the aluminum alloy to form an oxide film. As the oxide film forms, metal ions continuously deposit on the surface, gradually thickening the oxide film. With the increase in thickness, its conductivity gradually improves.
Characteristics of the conductive oxidation process include:
1. Good conductivity: The conductive oxide film has high conductivity, meeting the requirements of electronic products and other applications for electrical conductivity.
2. Good corrosion resistance: The conductive oxide film has good corrosion resistance, extending the service life of aluminum alloys in harsh environments.
3. Aesthetically pleasing: The surface of the conductive oxide film is smooth and uniformly colored, offering good aesthetic effects.
4. Environmentally friendly: The electrolyte solution used in the conductive oxidation process can be recycled, resulting in less environmental pollution.
II. Anodizing Process
Anodizing, also known as oxidation polishing, is a process that forms a uniform, dense oxide film on the surface of aluminum alloys. This process occurs in a specific electrolyte solution, where, through the action of an electric current, an oxidation reaction takes place on the surface of the aluminum alloy, forming an oxide film. The anodized film exhibits excellent corrosion resistance, wear resistance, and aesthetic appeal.
The principle of the anodizing process is similar to that of conductive oxidation; it involves the use of an electrolyte solution, where the aluminum alloy acts as the anode, undergoing oxidation due to the electric current. During anodizing, cations in the electrolyte solution accumulate near the anode and combine with metal ions on the surface of the aluminum alloy to form an oxide film. As the oxide film forms, metal ions continuously deposit on the surface, gradually thickening the oxide film.
Characteristics of the anodizing process include:
1. Good corrosion resistance: The anodized film has good corrosion resistance, extending the service life of aluminum alloys in harsh environments.
2. Good wear resistance: The anodized film has good wear resistance, enhancing the耐磨性of aluminum alloy surfaces.
3. Aesthetically pleasing: The surface of the anodized film is smooth and uniformly colored, offering good aesthetic effects.
4. Environmentally friendly: The electrolyte solution used in the anodizing process can be recycled, resulting in less environmental pollution.
In summary, both conductive oxidation and anodizing processes significantly enhance the performance and appearance of aluminum alloys. Conductive oxidation is primarily used to improve the electrical conductivity of aluminum alloys, while anodizing is mainly used to enhance their corrosion resistance and wear resistance. In practical applications, the appropriate process should be selected based on specific needs.