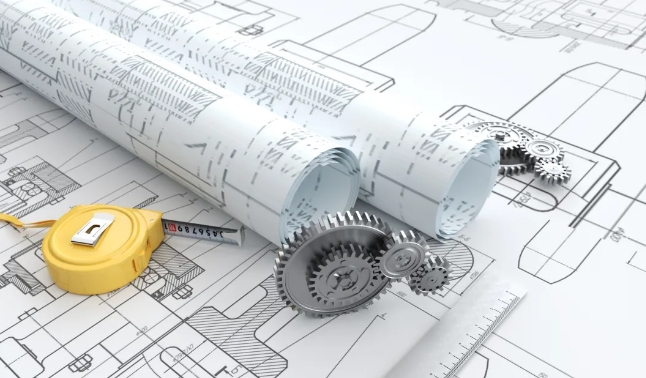
01 Cost-First Principle
The biggest feature of the design of non-standard products is small-scale production, single function, and limited adaptability. To "make money" from the beginning, we need to strictly control costs, which can be considered from the following aspects:
(1) R&D Cost
Try to assign experienced and capable professionals as the project leaders for non-standard product design projects. In terms of project staffing, it is necessary to minimize the number of personnel while ensuring their excellence. The project leader should not only have sufficient experience and ability in design but also be able to coordinate the team effectively. At the same time, they should also ensure the efficient operation of the team and keep R&D costs to a minimum.
(2) Procurement Cost
Procurement cost control also requires the active cooperation of R&D engineers. Try to make the selected components as general and standardized as possible and unify the suppliers of these components to form long-term and mutually beneficial strategic partnerships.
At the same time, negotiate favorable payment terms, such as quarterly or annual payments, to minimize the occupation of working capital.
(3) Outsourcing Cost
In terms of structural design, try to make functional components modularized, standardized, as much as possible. Although outsourcing processing, strive to scale up and batch these functional components and establish long-term and strategic cooperative relationships with manufacturers. Through long-term and stable cooperation, improve outsourcing efficiency and reduce outsourcing costs.
(4) Assembly Cost
This also involves the handling of non-standard design structures and the implementation of functional components and installation. Try to simplify, compact, and standardize the structure, and prefer to purchase instead of outsourcing, and prefer outsourcing instead of self-production.
Before assembly, fully explain and instruct the assembly technical staff and establish standard assembly processes and techniques to ensure a smooth assembly process.
(5) Debugging Cost
The debugging cost depends on the depth of project research and analysis before non-standard design and the expertise and experience of the project designer. It also relies on the on-site debugging engineer's ability to adapt and their proficiency in technology.
For non-standard design projects, make sure the best people are on the front lines, as they are the biggest guarantee for project success.
(6) After-sales Cost
The infinite increase of after-sales costs is one of the reasons why non-standard designs are expensive and also the most uncontrollable aspect.
Whether a project is profitable or not is largely focused on after-sales, and the control of this cost mainly lies in the design. We will make a more detailed analysis later.
02 Quality Assurance Principle
The quality assurance of non-standard products comes from two main aspects, and as long as these two aspects are controlled well, the product quality can be basically guaranteed:
(1) Engineer's Design Ability
For non-standard design, due to its nature of "one-time deal," there is no opportunity for trial and error and no budget for it. If we want to "make money" from the beginning, we need to strictly control costs. The control of costs can be considered from the following aspects:
(1) R&D cost
Try to assign experienced and capable professionals as the project leaders for non-standard product design projects. In terms of project staffing, it is necessary to minimize the number of personnel while ensuring their excellence. The project leader should not only have sufficient experience and ability in scheme design but also be able to coordinate the team effectively. At the same time, they should also ensure the efficient operation of the team and keep R&D costs to a minimum.
(2) Procurement cost
Procurement cost control also requires the active cooperation of R&D engineers. Try to make the selected components as general and standardized as possible and unify the suppliers of these components to form long-term and mutually beneficial strategic partnerships.
At the same time, negotiate favorable payment terms, such as quarterly or annual payments, to minimize the occupation of working capital.
(3) Outsourcing cost
In terms of structural design, try to make functional components modularized, standardized, as much as possible. Although outsourcing processing, strive to scale up and batch these functional components and establish long-term and strategic cooperative relationships